真空炉石墨模具是以高纯度石墨材料制成的精密热工部件,专为真空环境下的高温加工设计。其核心特性源于石墨材料的天然优势:熔点达3850±50℃,在3000℃惰性气氛中仍能保持结构稳定,配合低热膨胀系数特性,可实现高温急冷急热工况下的零裂纹运行。典型产品如T707系列密度达1.85g/cm³,肖氏硬度65,抗压强度115MPa,抗折强度51MPa,兼具机械强度与韧性。广泛应用于航空航天、汽车制造、冶金、机械等领域。在这些领域中,石墨模具用于制造各种高温合金、精密零件和特殊材料,为工业生产提供了重要的支持。
1、开裂问题
原因:
加热或冷却速度过快,导致热应力过大,使模具产生裂纹。例如在高温下迅速冷却,石墨模具内外温差大,收缩不一致。
石墨模具本身存在缺陷,如内部有微裂纹、气孔等,在使用时这些缺陷会扩展,导致开裂。
受到外力冲击,如在安装、取出工件过程中操作不当,使模具受到碰撞。
解决方法:
优化加热和冷却过程,采用缓慢的升温和降温速度,避免温度急剧变化。例如在加热时,先以较低的速率升温,使模具均匀受热,然后再逐步提高升温速度;冷却时,也采用类似的缓慢降温方式4。
在制造模具时,严格控制原材料质量和加工工艺,减少模具内部的缺陷。对石墨材料进行充分的烘干和预处理,去除水分和挥发物,降低其在高温下产生气体的可能性,从而减少因气体释放导致的开裂风险4。
在操作过程中要小心谨慎,避免对模具造成碰撞和冲击。使用合适的工装夹具来固定和取放模具,确保操作的平稳性。
2、氧化问题
原因:
真空炉内虽然处于真空环境,但在高温下,石墨仍可能与微量氧气发生反应,导致氧化。特别是在真空度不够或炉内气氛中含有杂质气体时,氧化现象更容易发生。
模具表面的保护涂层损坏或失效,无法有效阻止氧气与石墨接触。
解决方法:
提高真空炉的真空度,减少炉内氧气含量。定期检查和维护真空系统,确保其正常运行,保证炉内的真空环境稳定。
对石墨模具表面进行抗氧化处理,如涂覆抗氧化涂层。常见的涂层材料有金属氧化物、碳化物等,这些涂层可以在模具表面形成一层保护膜,阻止氧气与石墨接触,从而提高模具的抗氧化性能。
3、变形问题
原因:
高温下石墨的强度降低,在承受较大压力或自重的情况下容易发生变形。例如在烧结过程中,如果模具设计不合理或支撑不足,就可能导致变形。
模具的结构和尺寸设计不合理,没有考虑到热膨胀系数的影响。在加热过程中,由于不同部位的热膨胀量不同,会产生内应力,导致模具变形。
解决方法:
优化模具的结构设计,根据石墨的材料特性和使用要求,合理确定模具的形状、尺寸和壁厚。增加必要的支撑结构,提高模具的刚性和稳定性,以抵抗高温下的变形。
在模具制造过程中,充分考虑热膨胀系数的影响,预留适当的膨胀间隙或采取补偿措施。例如,在模具的连接部位采用弹性连接方式,允许一定程度的相对位移,以缓解热膨胀带来的应力。
4、磨损问题
原因:
在长期使用过程中,工件与模具表面不断摩擦,导致模具表面磨损。特别是对于一些硬度较高的工件,磨损会更加严重。
模具表面的粗糙度较高,增加了与工件的摩擦力,加速了磨损过程。
解决方法:
对模具表面进行抛光处理,降低表面粗糙度,减少摩擦系数。定期对模具进行修整和维护,及时修复磨损的表面,保持模具的精度和光洁度。
合理选择模具材料和热处理工艺,提高模具的硬度和耐磨性。例如,采用高强度、高耐磨性的石墨材料,或者对模具进行表面硬化处理,如渗碳、渗氮等。
5、粘模问题
原因:
工件与模具之间的粘结力较大,在脱模时容易导致粘模。这可能是由于模具表面不光滑、脱模剂使用不当或工件与模具的材料相互作用等原因引起的。
烧结过程中温度过高或时间过长,使工件与模具之间的结合力增强,增加了粘模的可能性。
解决方法:
改善模具表面的光洁度,使其更加光滑,减少与工件的粘结力。正确使用脱模剂,根据不同的工件材料和烧结工艺选择合适的脱模剂种类和涂抹方式,确保脱模剂能够均匀地覆盖在模具表面,并且不会对烧结过程产生不良影响。
优化烧结工艺参数,控制好烧结温度和时间,避免过度烧结导致粘模。在烧结前,可以对工件和模具进行适当的预热处理,使两者的温度更加接近,减少因温度差异而产生的热应力和粘结力。
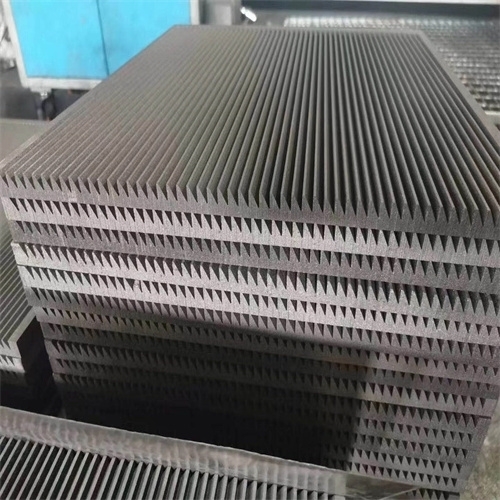